Generative Design, an iterative design exploration process that uses an AI-driven software program to generate a range of design solutions that meet a set of constraints. Unlike traditional design, where the process begins with a model based on an engineer’s knowledge, Generative Design begins with design parameters and uses AI to generate the model. The role of the engineer has evolved alongside technology. As design has come to rely more heavily on computer software, understanding how to manipulate digital tools to solve design challenges has become a central requirement for engineers working in all industries. Before generative design, engineers would conceptualize and test iterations using hands-on sketching and modeling.
The most common use for generative design algorithms today is structural optimization: creating parts that provide sufficient strength, stiffness, and fatigue resistance with the minimum of material. Such applications are common wherever weight is a primary consideration, such as in the design of internal structural parts for handheld tools (to improve ergonomics), sports equipment (to enhance performance), vehicles and aircraft (to reduce fuel consumption or increase payload), or any product where shipping weight is a significant cost driver.
Artificial Intelligence, Machine Learning and IoT act as the fundamentals and thereby help improve efficacy and output design factor. AI can quickly produce a high volume of concepts attuned to the requirements of the project. Using Generative Design, Engineers specify high-level performance requirements and general design frameworks and then relegate the details to the software. The process of defining these parameters can be particularly complex when characterizing novel materials or modelling hard-to-define problems and solution spaces. In a fundamental shift from traditional design processes, engineers will no longer need to create design solutions themselves. Instead, through generative design, they articulate and refine the environment in which design solutions can succeed.
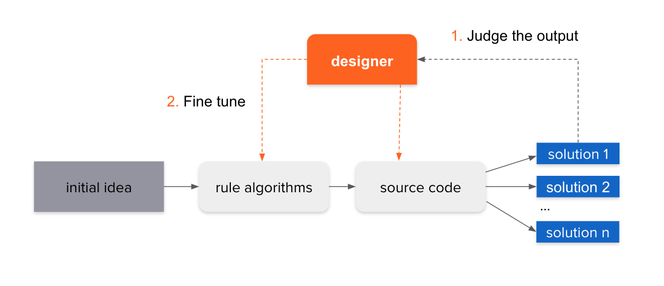
Generative Design applications exist across many industries from aerospace and architecture to manufacturing and consumer goods. Engineers who use generative design are often trying to solve complex engineering challenges. Such challenges include reducing component weights and manufacturing costs, scaling component customization, and optimizing performance.
3D printing works well with generative design because it provides a flexible, fast means of producing a three-dimensional, high-resolution model of one or more design iterations for a cost-effective final product. Generally, in economic terms, the cost-effectiveness of 3D printing increases alongside the complexity of a design iteration. Generative design algorithms often create highly efficient organic shapes with supporting latticework that are costly or even impossible to fabricate with conventional manufacturing technologies such as injection moulding or subtractive manufacturing tools like CNC machining. Advanced manufacturing tools like 3D printing—also known as additive manufacturing—are essential for the types of performance-sensitive applications where this optimization is compelling.
3D printing is more cost-competitive at lower production volumes because you do not need to reach an economy of scale to offset setup costs. Therefore, it facilitates the mass customization that generative design makes possible. As the cost of 3D printing continues to decrease and the variety of materials increase, 3D printing is becoming practical for small and mid-volume parts for more and more applications.
The Electric Vehicle and the Automotive Industry holds a prominent position in manufacturing with latest technologies and Innovations. Automotive electrical and electronic systems are becoming more complex, making the task of designing today’s cars much more difficult. Infotainment, comfort and convenience features, and even safety- and mission-critical systems such as steering and throttle control are accomplished through electrically powered computers, actuators, and sensors.
Electric vehicles will only increase this challenge. All-electric vehicles do not have the support of a supplemental source of power such as an ICE. All the power the vehicle needs is supplied by the energy stored in the batteries. As a result, the number and sophistication of the electronic features on an electric vehicle has a direct effect on the drive range and performance of the vehicle. ADAS systems often incorporate cameras, radar, and ultrasonic sensors to enable lane departure warning systems, automatic braking, and more. These systems are a constant drain on the battery as they are always active.
Generative design takes system definitions and requirements as input and generates architectural proposals for the logic, software, hardware, and networks of the E/E systems using rules-based automation. These rules capture the knowledge and experience of the veteran engineers to guide younger engineers throughout the design. Capturing this IP helps companies to develop both vehicle architectures and new generations of engineers as they learn and implement existing company knowledge.
A notable benefit of generative design is that it allows the simultaneous exploration, validation, and comparison of hundreds or thousands of design options. The software can display and compare design options in a way that enables engineers to quickly and efficiently find the ones that best meet a project’s parameters and needs. Generative design can create complex designs like organic features and internal lattices to leverage the unique design freedom offered by additive manufacturing technologies. It also offers the ability to consolidate parts, so a single complex geometry created by a generative algorithm and 3D printed can often replace assemblies of dozens of separate parts. Let us also discuss on the different software used today in the Market:
Fusion 360 from Autodesk
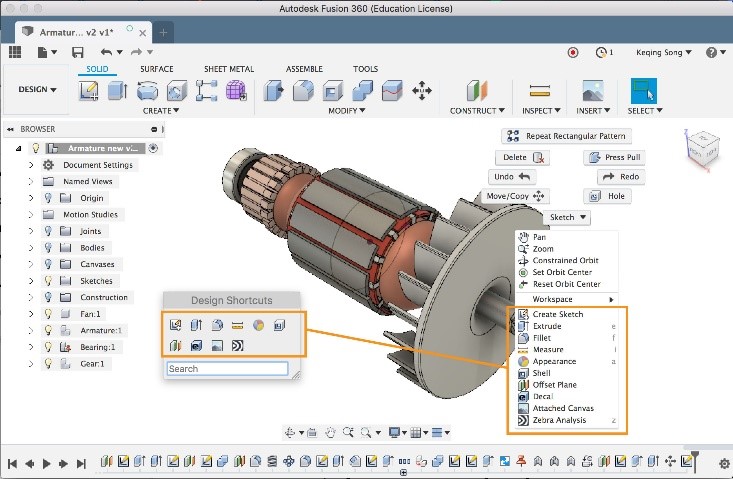
Fusion 360 offers users a powerful set of modelling tools, including sketching, direct modelling, surface modelling, parametric modelling, mesh modelling, rendering, and much more. Its generative design capabilities enable users to identify design requirements, constraints, materials, and manufacturing options to generate manufacturing-ready designs, all the while enabling users to leverage the power of machine learning and AI to review cloud-generated design outcomes based on visual similarities, plots, and filters.
Creo Generative Design from PTC
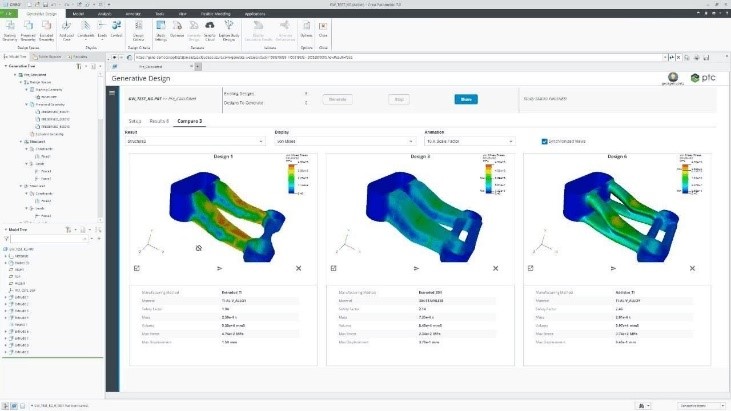
Leveraging the cloud, this software enables users to create optimized design concepts and simultaneously explore and test numerous design iterations quickly. It highlights the iterations that best match a user’s objectives based on design parameters the user sets. Within the Creo design environment, this software promises to generate high-quality, lower-cost, and manufacturable designs, all in less time than leading competitors.
nTop Platform from nTopology
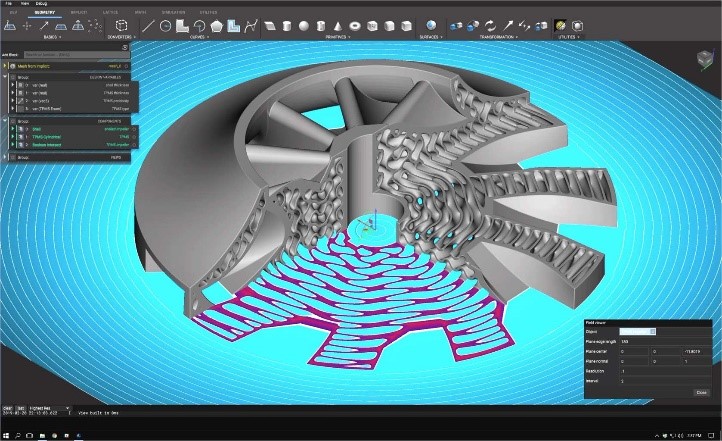
The nTop Platform software promises users complete control over every aspect of the optimization process and its outputs. Leveraging advanced generative tools, users can create custom, reusable workflows tailored to an application’s unique requirements. Featured capabilities of this program include unbreakable modelling and latticing operations, topology optimization, reusable design workflows, field-driven design, and mechanical-thermal finite element analysis simulations.
NX from Siemens
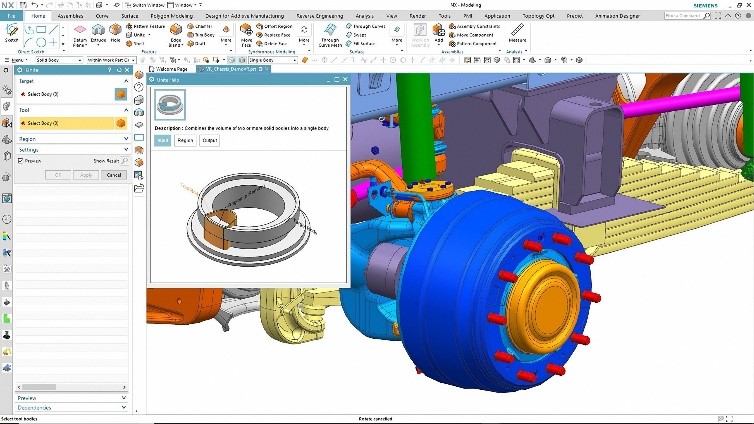
Beyond generative design, the main feature that NX offers is the digital twin technology, which promises users a flexible, powerful, and integrated solution to help them streamline the design and delivery of better products. NX combines design interoperability, validation, model-based definition, and more to help users move products through research and development faster and at lower costs while improving product quality.
MSC Apex Generative Design from MSC Software
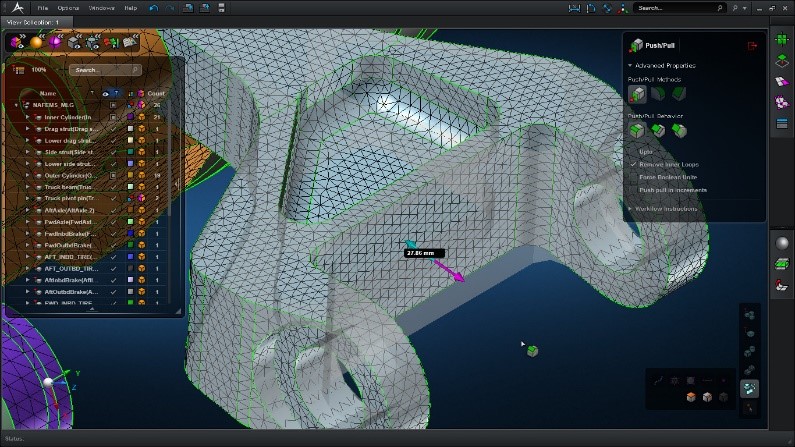
This program promises users an end-to-end solution for making high-precision metal components more quickly and with less human intervention than its competitors. MSC Software reports that users experience reductions in initial design and setup time by as much as 80 percent. At a glance, the software combines simplicity, automated design, import and validation, and direct output in one process.
Generative design technology is a culmination of the awesome power of AI, ML, and a designer’s talent. With the advent of high processing power and advanced scripting capabilities, this technology is surpassing its original constraints to give us amazing designs. The generated products are capable of following every specified requirement and constraint to provide us with truly innovative Computer-Aided Design models perfect for our needs. Today, there are still only a few industries that can actually benefit by lowering their overall costs. For example, Airbus shaved off 45% (30 kg) of the weight of a single part. The fuel consumption decrease equaled to removing 96,000 cars off the road for a year.
The development and spread of generative design have to go hand-in-hand with the availability of Additive manufacturing. Although the real potential will be unveiled in the future, we can see the first strides in the right direction. In the coming years, generative algorithms will continue to evolve, becoming more powerful, more widely applicable, and easier to use. As additional computing power becomes available, it will be possible to extend the approach beyond the part level to permit the optimization of assemblies and, ultimately, complete products.
By Mannu Mathew | Sub Editor | ELE Times
The post Generative Design is the novel design technology simplifying the relation between Computer and Engineer appeared first on ELE Times.
No comments:
Post a Comment